Wednesday, November 24, 2010
Zero Energy Home Virginia:Solar PV-show me the money!
Saturday, August 28, 2010
Tightening up to Zero: the Blower Door test Blowout!


A blower-door fan is sealed into an exterior doorway, all the house vents are temporarily sealed, and the calibrated fan blows air out of the house creating a pressure difference between the inside and outside, which draws air into all of the inadequately sealed cracks, holes and penetrations. A pressure sensing device is used to measure the rate of pressure change/leakage. The data is entered into a standardized formula and the number of Natural Air Changes per Hour (NACH) is derived. Typical production-built homes built under current building codes will score at about 0.5NACH or higher (one complete air change every two hours). A well built, near zero energy home aims for a score of 0.1-0.2NACH. EarthCraft Virginia officials, including Chuk Bowles, Technical Director (tending to the pressure monitor above) and KC McGurren, Executive Director, supervised the testing of our home this week.

Tuesday, August 3, 2010
Zero in on Geothermal HVAC in Virginia

But then lets not forget that buried loop I mentioned earlier. This involves 3200 feet of 3/4 inch high density polyethelene pipe buried in two 400 foot runs of trenches dug six feet deep and placed 10 feet apart. Suffice it to say that pretty much snaked over every available inch of our front, back and side yards. It looked like the mole from H_ll attacked our lot.

Friday, July 23, 2010
Insulating our way to Net-Zero: Loose-Fill Cellulose
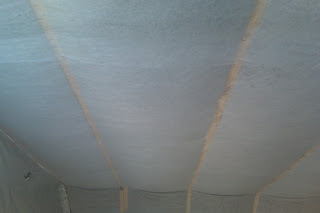


Saturday, July 10, 2010
Insulating our way to Net-Zero: Icynene


Note in the pictures that all ducting is being kept in conditioned space, increasing energy efficiency.
Sunday, July 4, 2010
Insulating our way to Net-Zero: Wet Spray Cellulose



Saturday, June 19, 2010
Richmond Virginia Zero Energy Home Progress & Appearance


Thursday, June 3, 2010
Net Zero Energy Virginia Home and best practices...


RainDrop’s innovative drainage channels keep water out of the wall system. The channels won’t crimp, collapse, or flatten, ensuring water will drain no matter how tightly cladding is nailed to the wall. Because it’s not perforated, RainDrop resists air and water infiltration. Plus it breathes to allow moisture vapor to escape. With its high tear resistance and translucent design, installation is quick and easy with no job site waste. And it stays UV-stable up to 4 months. RainDrop is an ideal secondary weather barrier for fiber cement, vinyl, foam-backed vinyl, and wood sidings and meets the National, Standard, Uniform and International Building Code requirements for air barriers, moisture protection barriers and weather-resistive barriers. It is used on top of the SIS and behind any of the areas to be covered with shingling.
Saturday, May 29, 2010
The window to a zero energy home, Richmond, VA style...

When it came to window choices, there was a lot to consider, because as you increase the tightness and the insulation level of your home, the glazing makes a greater impact on energy usage. And our particular home design has a lot of windows! Looking to the Efficient Windows Collaborative (EWC) for guidance, the 2009 Energy Star standards for Virginia suggested windows with a U-factor (the rate of non-solar heat loss or gain
through a whole window assembly) of .40 and a SHGC (the Solar Heat Gain Coefficient is the fraction of incident solar radiation admitted through a window) of <.40. But our EarthCraft builder reminded us that the EnergyStar standards were going to be tightened starting in 2010, so we set out in search of better windows. The new Virginia Energy Star standards are a U-factor of .32 and a SHGC of <.40, but few suppliers had windows available reflecting the new values yet. After some creative searching, Mark found us PlyGem MW Pro Series windows with a U-factor of .29 and SHGC of .25 for only $400 more than 2009 rated windows. These are vinyl clad PVC construction, 20 year, double pane, argon gas-filled, low-E glass windows with a Warm Edge technology ( the Warm Edge glass spacer system reduces thermal transfer around the glass perimeter by utilizing a unique U-shaped channel to separate glass panes and interrupt the natural flow of heat to cold). Hopefully the added insulation they provide will reduce the load on our geothermal HVAC system. We are hoping that the lower SHGC will work well, as we have a lot of southeast facing glazing on the back of our house, which because of solar sighting, has little shade in the summer, making excess heat gain in hot muggy Virginia a potential problem. Oh, and that door you see there, that is the Therma-Tru Classic-Craft® Mahogany(waiting to be stained) fiberglass front door, which is also EnergyStar rated. Have to have all the portals covered...
Monday, May 24, 2010
Solar PV arrives at the Virginia zero energy home!




Wednesday, May 12, 2010
ZEH, SIS, and other energy-friendly acronyms to know
The garage is not insulated, but covered with WEATHERMATE™ Plus – Housewrap to serve as an air and moisture barrier. It is significantly superior in water resistance, air porosity, vapor permeability and tear resistance than the more commonly used Tyvek. It also possesses prolonged UV ray resistance, allowing it to be exposed up to 120 days before significantly degrading (hopefully our garage will not test that limit).

Monday, May 3, 2010
ZEH Virginia, its all in the little things


Saturday, May 1, 2010
ZEH design blueprint
Sunday, April 25, 2010
Starting the envelope

Saturday, April 17, 2010
An enlightening experience...
Wednesday, April 7, 2010
A Greener Foundation

Wednesday, March 31, 2010
Wow.. it's going to really happen!!

Saturday, March 27, 2010
ZEH: it's a system
...it is basically designed as a single story home, with some bonus rooms upstairs...it will be all brick with a semi-detached garage (the why of that comes later)...the walls will be R16 and the attic R38...the walls will use wet spray cellulose and the attic loose cellulose...a conditioned crawl space...we are also using a new product on the outside of the stud walls, Dow Styrofoam SIS, (structural insulated sheathing) which will be taped, forming an air/vapor barrier, an extra layer of insulation, a shield against thermal bridging of the studs, and a structural element...pretty cool...with respect to the R levels, they are more than sufficient for our climate, as the wet spray cellulose significantly increases the thermal mass of the house... along with the tightness of the house (we aim for less than a .20 Natural Air Exchanges per Hour blower door result and a less than 4% of floor area served leakage to outside duct test result; an ERV will be installed for ventilation), the increased thermal mass may even eliminate the need for a setback thermostat, as the temperature of the house should remain incredibly stable...we are going to look into cool roofs/radiant heat barriers, but setting up the heating/coolng "firewall" at the attic floor may be more cost effective....
...we are looking at double pane, vinyl clad, low E, argon windows, with U value of .33 and SHGC of.30...we are looking into a new model with a U below .30, getting a price difference on that...
...Caroma (the reviews say they never clog) 1.28/0.8 dual flush toilets to save water...
...the HVAC system is proposed to be a Comfortaire GeoMax2 geothermal heat pump of 4 ton capacity with desuperheater rated @ 23.7/16.6 EER & 4.0 COP...hot water will be pre-heated by the desuperheater and then go to a 98% efficient Navien tankless condensing water heater with a built in recirculation pump & mini buffer tank for a digital timer controlled recirculation loop to prevent the dreaded "cold water sandwich" you can get with tankless water heaters...the solar grid-connected PVC array will consist of 20 Schuco Monocrystalline 210 panels (4.2kW) and a SunnyBoy inverter mounted on a true south oriented garage roof...
We will begin to look at each of these features as the build progresses, analyzing their benefits and potential assets and seeing how they may complement (and hopefully not compromise) the "system". Stay tuned.