Saturday, January 21, 2012
ZEH-Richmond's performance at year's end
So we have had a solid, representative year in our house now and we wanted to update its real-life performance. Our total energy bill for 2011 was $954, $532 for electricity and $422 for natural gas. The electric bill reflected the cost for heating, cooling, lights, appliances, etc. The highest monthly bill was $125 in the winter, while five months (the "shoulder" seasons in the spring and fall) were effectively "zero". Our natural gas bill reflected energy used to heat water, cook and operate the gas fireplace. The highest bill was $55 in the winter, while the lowest was $20 in the summer. We did make thoughtful attempts to run the house in an energy efficient fashion, opening & closing windows to take advantage of natural heating and cooling effects, and maintaining temperatures of 69day/68night (the geothermal system does not like big heat swings) in the winter and 76-78 in the heat of the summer. Our SRECs have turned out to be a bust. The initial contract we signed got "lost" in the system, and the replacement contract was only offered at a variable auction rate. The bottom subsequently fell out of the SREC market due to regulatory and political decisions that are too complex to explain here. As a result, we received a nominal $80 this year for SRECs, putting our net annual energy bill at $874. Given we have Watersense rated water fixtures and low flow toilets in the house, it is worth adding that our total annual water & sewage bill was $714. The lowest monthly bill was $31 and the highest was $90 (fall replanted lawn irrigation effect).So in sum, our average monthly energy bills were $73, our average water & sewage bill was $59 and our average total monthly utility bill was $132. In comparison, the average monthly energy bill for a (smaller) US home was approximately $180. We didn't make "zero", for a number of reasons I will address in a later blog, but I feel that a monthly energy bill for about the price of a dinner and a movie for the two of us is a pretty fair result!
Wednesday, November 24, 2010
Zero Energy Home Virginia:Solar PV-show me the money!
Everyone is always curious about the cost of solar PV and its "payback". So here's the numbers in black and white. The 4.2kW system cost $30,973 installed. The Commonwealth of Virginia gave us a rebate of $7189, and the Feds will give us a tax credit of $7135, resulting in a net cost of $16,649. We are selling the SRECs (Solar Renewable Energy Credits) for $200/yr. each (thanks to Cory, from olddominioninnovations.com, for brokering this) , for a total of approximately $800-1000 per year. The panels are generating from 11-25kWh per sunny day (less right now, with the shorter days & the sun lower in the sky; more come the long, high-in-the-sky days of early summer). So there it is, in black & white. I will leave it to each of you to decide how the "payback" looks to you, as the ways of calculating it are as myriad as the colors in the rainbow! All I know is that I love watching the digits in the Dominion Power digital meter get smaller!
Saturday, August 28, 2010
Tightening up to Zero: the Blower Door test Blowout!


A blower-door fan is sealed into an exterior doorway, all the house vents are temporarily sealed, and the calibrated fan blows air out of the house creating a pressure difference between the inside and outside, which draws air into all of the inadequately sealed cracks, holes and penetrations. A pressure sensing device is used to measure the rate of pressure change/leakage. The data is entered into a standardized formula and the number of Natural Air Changes per Hour (NACH) is derived. Typical production-built homes built under current building codes will score at about 0.5NACH or higher (one complete air change every two hours). A well built, near zero energy home aims for a score of 0.1-0.2NACH. EarthCraft Virginia officials, including Chuk Bowles, Technical Director (tending to the pressure monitor above) and KC McGurren, Executive Director, supervised the testing of our home this week.

Tuesday, August 3, 2010
Zero in on Geothermal HVAC in Virginia
In a typical home, heating and cooling represents 56% of energy usage, the largest piece of the energy consumption pie. To strive for a zero energy home, it is logical to try to drive this heating and cooling load down as low as possible. Although we initially considered using solar thermal radiant heating, we soon abandoned this idea in favor of a geothermal heat pump in combination with solar PV. Solar PV is more "plug and play" than solar thermal, and when combined with geothermal, serves as one low energy solution to both heating and cooling needs, both of which are high demands in the temperate Virginia climate. A ground source geothermal heat pump uses the relatively constant temperature of the ground six feet below the surface, which in Virginia is estimated to be approximately 60 degrees, to heat or cool the home. An antifreeze solution is piped through loops in the ground where, depending on the season, heat is either absorbed and used to heat the home, or the unwanted heat from the home is expelled. As in a conventional heat pump, a compressor and an air handler are used to condense and distribute the heat exchange. A geothermal heat pump does not produce heat, but rather it extracts and moves heat. Where the most efficient gas furnace may approach 97% efficiency, a geothermal heat pump may approach 400% efficiency, in effect, extracting 4 units of heat energy for each unit of energy expended. Research suggests that a geothermal heat pump may result in energy savings of 69% over gas heat and 40% over air to air heat pump heat. Jim Satterfield of HVAC by JM LLC worked closely with our builder to assess our projected heating and cooling loads and recommended a 4 ton Comfort-Aire GeoMax2 split unit connected to 3200 feet of buried loop. The GeoMax2 is a rebranded Climatemaster Tranquility 27 Series, which has an EER rating of 16.6/23.7 and COP rating of 3.7/4.2, some of the highest
ratings available. In comparison, Energy Star requirements for geothermal ground source heat pumps are 14.1 EER and 3.3 COP. The two stage compressor and variable speed fan coil contribute to the heightened efficiency while its reliance on R410-A refrigerant protects the ozone layer. The GeoMax2 includes a desuperheater, which uses excess heat to pre-heat your hot water, a nice added benefit. This a split unit, which means that the refrigerant/ compressor unit is seperated from the air handler unit, allowing them to more easily fit in the safety of the conditioned crawl space. The refrigerant/compressor unit is a small gray box about the size of a small bedside table. Once again, great things come in small packages!

The air handler is the same type of blower/ducting
But then lets not forget that buried loop I mentioned earlier. This involves 3200 feet of 3/4 inch high density polyethelene pipe buried in two 400 foot runs of trenches dug six feet deep and placed 10 feet apart. Suffice it to say that pretty much snaked over every available inch of our front, back and side yards. It looked like the mole from H_ll attacked our lot.
And in this case it was a
big bright orange one!

Friday, July 23, 2010
Insulating our way to Net-Zero: Loose-Fill Cellulose
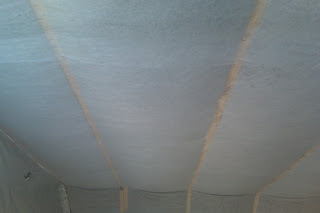

The last piece of the insulation puzzle is wet-spray cellulose's "poor relative", loose-fill cellulose. Loose-fill cellulose is made of up to 85% recycled paper and is sprayed dry with air, providing an R-value of 3.8 and blocking air leakage. Less expensive than both Icynene and wet-spray cellulose, our builder used it primarily in accessible, flat areas, sometimes using netting to hold it in place or offer support.
And the last piece of the insulation puzzle, would be fiberglass. To quote our builder, "in the inside walls for inexpensive sound insulation, that is the only place you will find fiberglass in one of my homes." He exaggerated a little, as he also used it (CertainTeed DRYRight) in the outside eaves, to form a barrier to spray the cellulose against. His opinion is that fiberglass is poorly suited to do its primary job, to provide insulation and to prevent air infiltration. To accomplish these tasks, the fiberglass must be installed perfectly, fitted precisely into all the nooks and crannies and sealed consistently around each and every opening and penetration. This is very time-consuming, labor intensive and challenging, as anyone who has attempted to apply fiberglass batt insulation can attest. It also tends to lose R-value across time and offers minimal thermal mass.

Saturday, July 10, 2010
Insulating our way to Net-Zero: Icynene


Another integral part of creating a well sealed and insulated space involved the use of Icynene spray foam insulation. Icynene is a 100% water-blown insulation that sprays on as a liquid and immediately expands to 100 times its volume in soft foam that fills every crack and crevice while providing a flexible seal and a R-3.7 insulation value. It does not out-gas or emit any harmful fumes and it retains a stable R-value across time. It is an open cell foam, so it does not block the movement of water vapor. Icynene is a petroleum-based product (Icynene-R is a new product based on castor oil)that is a flame retarding material that will be consumed by flame, but contributes no fuel and will not sustain fire upon removal of the flame source. It must be covered by an approved thermal barrier, which our builder will accomplish by seperating it from living space with drywall.
More expensive than wet-spray cellulose, but less expensive than closed cell spray foam, our builder chose to selectively use it in hard to access or otherwise challenging areas, like the vaulted ceiling, where it clings tightly in place, helping form a continuous, insulating air barrier. Seven inches were sprayed along the roofline, for an R-25 insulation rating. EarthCraft specs say R-20 Icynene is equal to R-30 of fiberglass or cellulose on vaulted surfaces.
Note in the pictures that all ducting is being kept in conditioned space, increasing energy efficiency.
Sunday, July 4, 2010
Insulating our way to Net-Zero: Wet Spray Cellulose

Our builder put a lot of thought into deciding what insulation to put where, balancing effectiveness against cost. One of his favorite products is wet-spray cellulose insulation, in this case from Applegate Insulation, a product that requires one fifth of the energy needed to produce an equivalent amount of fiberglass. Made from 85% recycled paper content, largely newspaper, and treated for fire and mold resistance with borate and with a dry adhesive, it is sprayed under pressure into the cavity with a small amount of water, completely filling all the nooks and crannies, reducing the flow of heat and virtually eliminating air infiltration.
After completely filling the cavity, a rotating stud scrubber brush is run over the area, leveling it even with the tops of the studs. The cellulose will dry over the next 24 hours, becoming firmer to the touch. No dangerous outgassing is involved, as it does not contain any formaldehyde or respirable microscopic fibers.

The finished surface is quite smooth and spongy to the touch, and the 3.5" of cellulose provides an R-value of 13.3, which when added to the R-3 of the SIS (Dow Structural Insulated Sheathing) on the outside, results in an overall stable R-value of 16.3 for the walls. Our builder believes that the superior air sealing power and the added thermal mass provided by the wet spray cellulose make that R-value a conservative estimate. It is notable that contrary to initial impressions, wet spray cellulose is quite fire retardant, a result of both the fire retardants applied to the paper and its heavy oxygen-limiting density, providing up to a 50% increase in fire resistance. It is also a very good product with respect to air quality, as indicated by the American Lung Association of Virginia choosing to use it in it's Breathe Easy headqu
arters.

Subscribe to:
Posts (Atom)